Heim joints, also known as rod ends or spherical rod ends, are essential components in various mechanical systems. They offer a versatile means of connecting rods or linkages, allowing for angular motion while transmitting force. Understanding how Heim joints are made provides valuable insight into the intricacies of their manufacturing process and sheds light on the high precision and engineering involved. In this article, we delve into the fascinating world of Heim joints, exploring their creation from raw materials to the final product.
Step 1: Material Selection
The manufacturing process of Heim joints begins with the careful selection of suitable materials. Common choices include high-quality steels such as alloy steel, stainless steel, or carbon steel. These materials offer excellent strength, corrosion resistance, and durability, ensuring that the resulting Heim joints can withstand the demanding mechanical applications they are designed for.
Step 2: Forging
The selected raw material undergoes a forging process to shape it into the desired Heim joint configuration. Forging involves subjecting the material to high temperatures and applying controlled pressure to shape it through plastic deformation. This process enhances the material's grain structure, improving its mechanical properties and ensuring superior strength.
Step 3: Machining
After forging, the partially formed Heim joints undergo machining operations to achieve precise dimensions and surface finishes. Advanced CNC (Computer Numerical Control) machines are commonly used for this purpose. CNC machining ensures accuracy and repeatability, allowing for complex geometries and intricate features to be machined with high precision. The machining process includes operations such as turning, drilling, milling, and threading to create the necessary features and prepare the joint for assembly.
Step 4: Heat Treatment
To further enhance the strength and durability of Heim joints, heat treatment is often employed. The forged and machined components are subjected to controlled heating and cooling cycles. This process alters the material's microstructure, improving its hardness and toughness. Heat treatment techniques such as quenching and tempering are commonly used to achieve the desired mechanical properties, ensuring the Heim joints can withstand the stresses they will encounter during operation.
Step 5: Surface Coating
To protect the Heim joints from corrosion and extend their lifespan, various surface coatings are applied. These coatings may include electroplating, powder coating, or specialized coatings such as zinc or nickel plating. The coating process involves carefully cleaning the surfaces and applying the coating material using techniques like electrostatic deposition or immersion. This additional layer not only enhances the aesthetics of the Heim joints but also provides crucial protection against environmental factors.
Step 6: Assembly and Quality Control
In the final stage of the manufacturing process, the various components of the Heim joint are assembled. This typically involves inserting the spherical bearing or ball, along with necessary washers, spacers, and seals, into the joint body. The assembly is carefully performed to ensure proper alignment and smooth movement. Once assembled, each Heim joint undergoes rigorous quality control inspections to ensure it meets the required specifications and performance standards. Testing may involve checking dimensions, load capacity, range of motion, and overall functionality.
The creation of Heim joints involves a meticulous manufacturing process that combines metallurgical expertise, precision machining, and stringent quality control. From material selection to forging, machining, heat treatment, surface coating, and final assembly, every step contributes to producing Heim joints with exceptional strength, durability, and functionality. These versatile components play a vital role in a wide range of applications, including automotive, aerospace, industrial machinery, and robotics, enabling smooth motion and reliable force transmission. Understanding the manufacturing process behind Heim joints provides us with a deeper appreciation for the engineering prowess and attention to detail required to create these fundamental mechanical components.
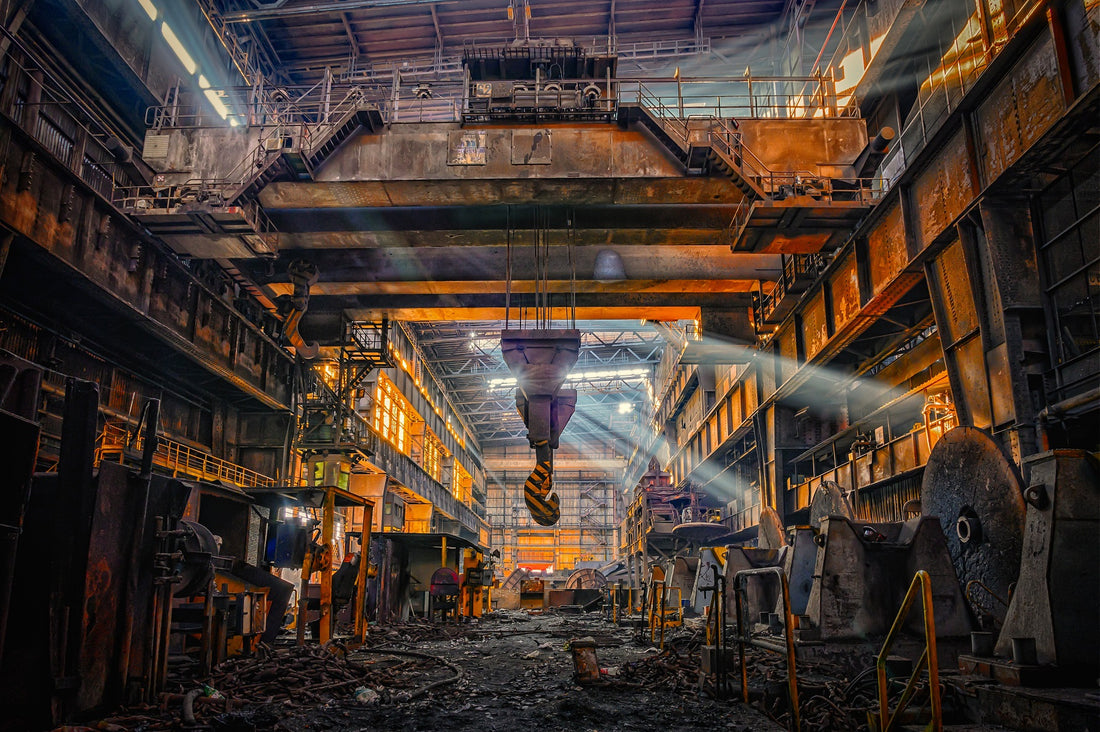